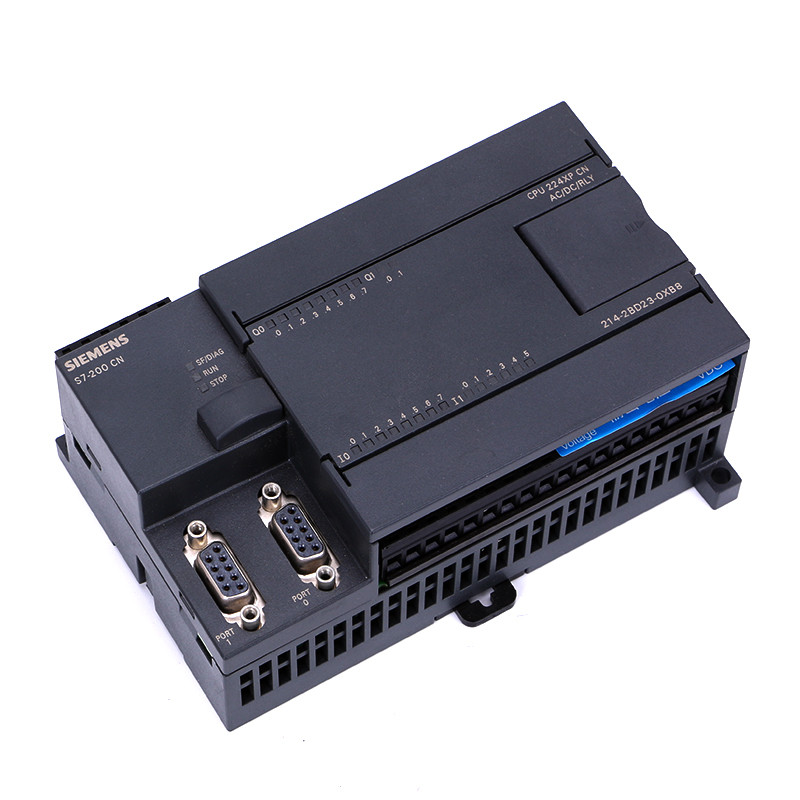
A Programmable Logic Controller (PLC) is an electronic device specifically designed for industrial automation. It can automate and monitor various equipment and production processes on the factory floor, and perform complex logical operations based on preset programs to achieve automated production.
Working Principle of PLC
The working principle of a PLC is to load a program into the controller, and then, based on the program's instructions, process input signals to control the output signals of devices. The PLC controller mainly consists of the processor, input modules, output modules, and communication modules. The input module converts input signals (such as sensor signals) into digital signals and sends them to the processor; the processor processes the input signals based on the program's instructions and performs logical operations to output control signals; the output module converts the digital signals output by the processor into working voltages or other outputs to control devices. The communication module enables data exchange between the PLC and other devices or systems, offering real-time monitoring and remote control capabilities.
Features of PLC
The main features of a PLC include the following aspects:
- Programmability: PLCs can implement different control logics and functions by writing and modifying programs, providing great flexibility.
- Reliability: PLCs usually use real-time operating systems and reliable hardware designs, ensuring stable long-term operation with low failure rates.
- Expandability: PLCs can be expanded by adding I/O modules, communication modules, etc., to meet different control needs.
- Flexibility: PLCs support various control methods, such as open-loop control, closed-loop control, position control, etc., offering powerful control capabilities in different application scenarios.
- Efficiency: PLCs use high-speed CPUs and optimized program designs to achieve efficient control and data processing, with fast response times.
- Ease of Maintenance and Operation: PLCs typically have simple, clear operating interfaces and are easy to maintain. Diagnostic and debugging functions help users quickly identify and resolve faults.
Advantages and Disadvantages of PLCs
Advantages of PLCs:
- High Reliability: All components of a PLC are subject to strict quality assurance and testing, making them highly reliable and stable.
- Programmable: PLCs have an independent, modular design that allows users to freely write control programs, offering high flexibility.
- Strong Expandability: PLC control systems can be expanded and modified with changes in process flows and production lines by adding new modules or subprograms.
- High Operational Efficiency: PLCs can achieve fast, efficient, and precise control, reducing energy consumption and improving production efficiency.
- Good Debugging Capabilities: PLCs have powerful self-diagnosis and fault feedback functions that help users quickly locate issues and debug the system.
Disadvantages of PLCs:
- Complex Programming: PLC programming requires certain professional skills and experience, which can be difficult for beginners or non-experts.
- High Cost: PLC equipment is usually expensive, requiring a significant investment.
- Poor Maintainability: Maintaining PLC equipment requires specialized skills and equipment, and is more difficult than for simpler systems, requiring professionals for upkeep.
- Limited Flexibility: PLC control systems require pre-written control programs. For unforeseen situations, the program may need to be rewritten, which is less flexible compared to manual control.
Principles and Recommendations for Selecting a PLC
When selecting a PLC, the following principles should be considered:
- Consideration of the Application Environment: PLCs should be installed in relatively stable environments. Factors such as temperature, humidity, dust, and vibration need to be considered when selecting a PLC product that matches the environment.
- Control Requirements: The PLC choice should be based on the control system’s needs, including the number of input and output points, memory capacity, processing speed, control range, and control logic.
- Programmability and Expandability: Choose a PLC with high programmability and expandability so the system can be upgraded and expanded as needed.
- Stability and Reliability: The stability and reliability of a PLC are crucial to the system’s operation. It is important to select products with high stability and reliability.
- Technical Support and Service: Choose a reliable supplier that offers comprehensive technical support and services to resolve any issues during operation.